Part of a series of articles titled Lowell, Story of an Industrial City.
Article • Lowell, Story of an Industrial City
Lowell, Story of an Industrial City: Making Textiles
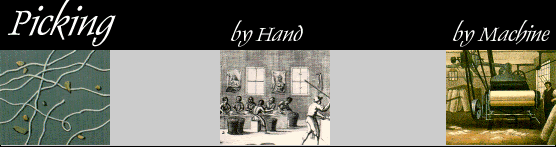
National Park Service
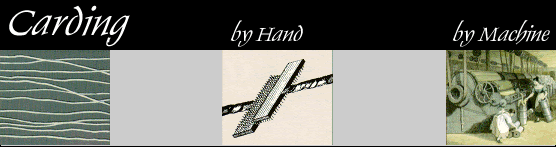
National Park Service
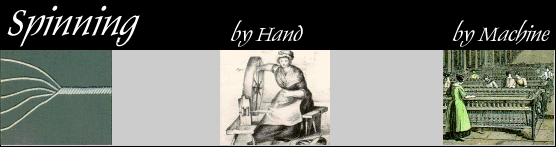
National Park Service
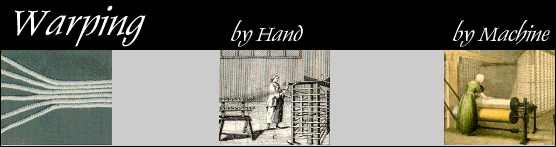
National Park Service
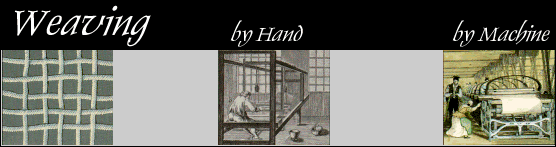
National Park Service
Last updated: June 15, 2018