The abutments blocks are made of heavily reinforced concrete that was pre-cast at the supplier’s facility in Harrisburg, Oregon and then transported to site. Each block weighs approximately 44,000 pounds.
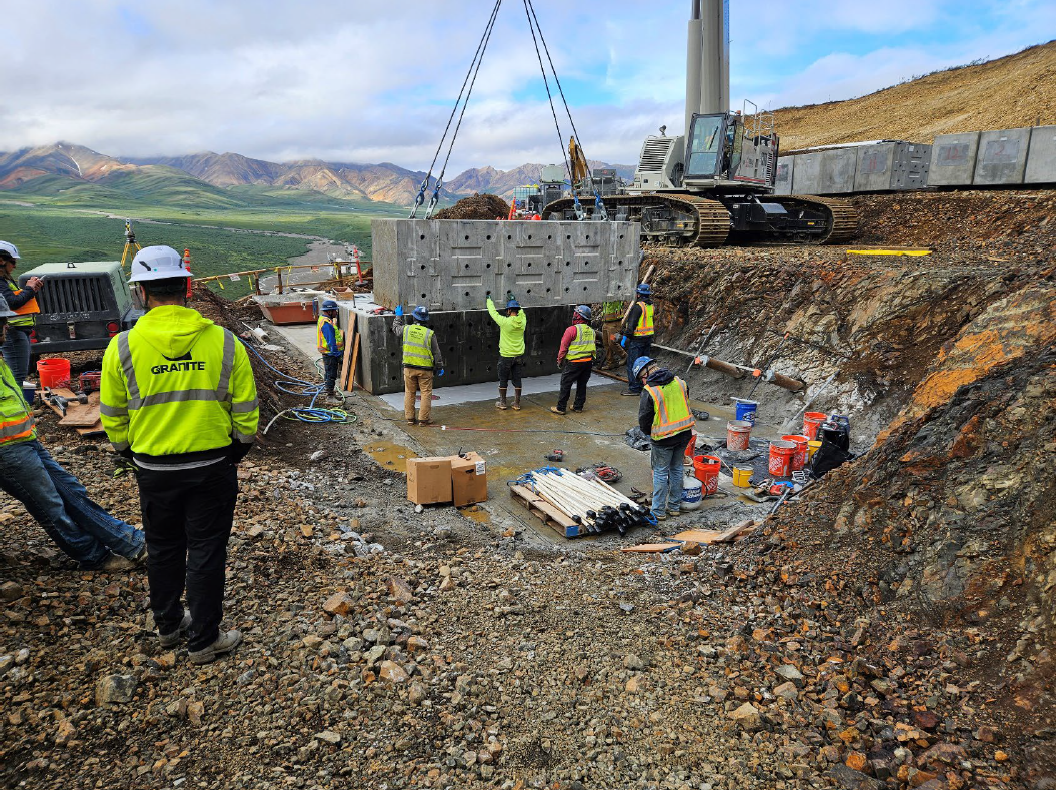
After all of the 15 blocks are placed, they’ll be joined together by a process known as post-tensioning. Twenty-seven high-strength steel cables (each consisting of 9 individual steel wires or “strands”) will be threaded through the 27 holes you can see in the side of each of the blocks, extending from one end of the abutment to the other. One end of each cable will be anchored to one end the abutment and the other end of the cable will be drawn tight (tensioned) with a hydraulic jack to a force of 395,000 pounds. Once the proper tension is achieved in each cable, the tensioned end is also anchored. Once all cables are tensioned, the holes in the abutment will be filled with cementitious grout, which protects the cables from corrosion. The combined tension force of all 27 cables squeezes the abutment blocks together, making them act essentially as one monolithic block to uniformly distribute the massive weight of the bridge to the underlying rock.