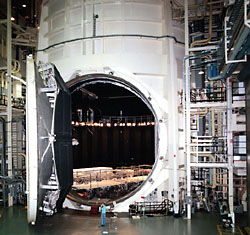
Located at Building 32 at the Lyndon B. Johnson Space Center in Houston, Texas, the Space Environmental Simulation Laboratory (SESL) was part of the manned spacecraft program of the United States. The SESL was designed, built, and used to conduct thermal-vacuum testing for all United States manned spacecraft of the Apollo era. The large size of both chambers in the SESL meant that full scale flight hardware could be tested for a variety of design and development programs involving such factors as operating temperatures, fluid leak rates, changes in absorptive or emissive properties of thermal coatings and other materials. The testing was absolutely essential to man rate, a higher safety level used for manned aviation operations, flight hardware. The safety of the astronauts and the success of the manned space program depended on information that resulted from these tests in the SESL.
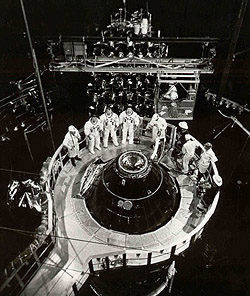
Since it was constructed in 1965, the SESL has tested all Apollo command and service modules, Apollo lunar modules, spacesuits for extra-vehicular activity, the Skylab/Apollo telescope mount system, various Space Shuttle systems, the Apollo/Soyuz docking module and various large scale scientific satellite systems such as the parabolic reflector subsystem of the Applications Technology Satellite. The thermal vacuum testing done at the SESL since 1965 has been a significant factor contributing to the success of both the manned and unmanned space program of the United States.
The SESL Chamber A is the largest of the Johnson Space Center thermal-vacuum test facilities. Its usable test volume and high-fidelity space simulation capabilities are adaptable to thermal-vacuum tests of a wide variety of test articles. The major structural elements of the chamber are the rotatable floor, the 40-foot diameter access floor and the dual manlocks at the floor level and at the 31-foot level. Test articles are normally inserted into the chamber by means of overhead cranes and a dolly and track. The dual manlocks are chambers that provide a means for the test crew to move from ambient air pressure to the thermal-vacuum environment and back. When the inner door is bolted, either of the manlocks can be used as an altitude chamber for independent tests. Chamber B, the smaller man-rated chamber, has the same basic capability as Chamber A and can accommodate a variety of smaller scale tests more economically and with faster responses. Major structural elements of the chamber are the removable top head, the fixed chamber floor, and a dual manlock at the floor level.
Visit the National Park Service Travel American Aviation to learn more about Aviation related Historic Sites.
Last updated: August 28, 2017